直线驱动机构
通常,齿条是固定不动的,当齿轮传动时, 齿轮轴连同拖板沿齿条方向做直线运动, 这样, 齿轮的旋转运动就转换成为拖板的直线运动, 如图1所示。拖板是由导杆或导轨支承的。 该装置的回差较大。
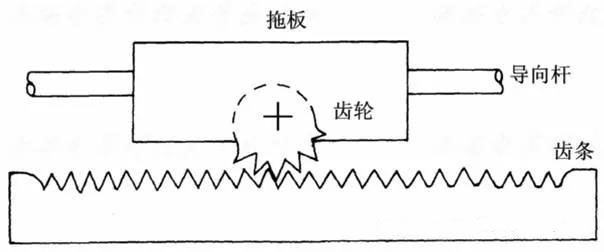
图1 齿轮齿条装置
普通丝杠驱动是由一个旋转的精密丝杠驱动一个螺母沿丝杠轴向移动。 由于普通丝杠的摩擦力较大, 效率低, 惯性大, 在低速时容易产生爬行现象, 而且精度低, 回差大, 因此在机器人上很少采用。
3. 滚珠丝杠
在机器人上经常采用滚珠丝杠, 这是因为滚珠丝杠的摩擦力很小且运动响应速度快。由于滚珠丝杠在丝杠螺母的螺旋槽里放置了许多滚珠,传动过程中所受的摩擦力是滚动摩擦, 可极大地减小摩擦力,因此传动效率高,消除了低速运动时的爬行现象。在装配时施加一定的预紧力,可消除回差。
如图2所示, 滚珠丝杠里的滚珠从钢套管中出来, 进入经过研磨的导槽, 转动2~3圈以后, 返回钢套管。 滚珠丝杠的传动效率可以达到90%, 所以只需要使用极小的驱动力, 并采用较小的驱动连接件就能够传递运动。
图 2 滚球丝杠副
旋转驱动机构
1. 齿轮链
齿轮链是由两个或两个以上的齿轮组成的传动机构。它不但可以传递运动角位移和角速度, 而且可以传递力和力矩。 现以具有两个齿轮的齿轮链为例, 说明其传动转换关系。其中一个齿轮装在输入轴上, 另一个齿轮装在输出轴上, 如图3所示。
图3 齿轮链机构
使用齿轮链机构应注意两个问题:
一是齿轮链的引入会改变系统的等效转动惯量, 从而使驱动电机的响应时间减小, 这样伺服系统就更加容易控制。输出轴转动惯量转换到驱动电机上, 等效转动惯量的下降与输入输出齿轮齿数的平方成正比。
二是在引入齿轮链的同时, 由于齿轮间隙误差, 将会导致机器人手臂的定位误差增加; 而且, 假如不采取一些补救措施, 齿隙误差还会引起伺服系统的不稳定性。
通常, 齿轮链转动有以下几种类型, 如图4所示。
其中圆柱齿轮的传动效率约为90%, 因为结构简单, 传动效率高,圆柱齿轮在机器人设计中最常见;斜齿轮传动效率约为80%,斜齿轮可以改变输出轴方向; 锥齿轮传动效率约为70%, 锥齿轮可以使输入轴与输出轴不在同一个平面, 传动效率低; 蜗轮蜗杆传动效率约为70%,蜗轮蜗杆机构的传动比大, 传动平稳,可实现自锁,但传动效率低,制造成本高, 需要润滑;行星轮系传动效率约为80%,传动比大, 但结构复杂。
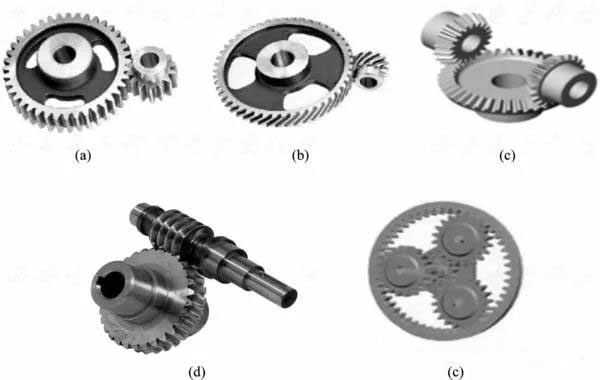
图4 常用的齿轮链
(a) 圆柱齿轮; (b) 斜齿轮; (c) 锥齿轮; (d) 蜗轮蜗杆; (e) 行星轮系
2. 同步皮带
同步皮带类似于工厂的风扇皮带和其他传动皮带, 所不同的是这种皮带上具有许多型齿, 它们和同样具有型齿的同步皮带轮齿相啮合。
工作时, 它们相当于柔软的齿轮, 具有柔性好, 价格便宜两大优点。另外, 同步皮带还被用于输入轴和输出轴方向不一致的情况。
这时, 只要同步皮带足够长,使皮带的扭角误差不太大, 则同步皮带仍能够正常工作。在伺服系统中, 如果输出轴的位置采用码盘测量, 则输入传动的同步皮带可以放在伺服环外面, 这对系统的定位精度和重复性不会有影响, 重复精度可以达到1 mm以内。 此外, 同步皮带比齿轮链价格低得多, 加工也容易得多。 有时, 齿轮链和同步皮带结合起来使用更为方便。
虽然谐波齿轮已问世多年, 但直到最近人们才开始广泛地使用它。 目前, 机器人的旋转关节有60%~70%都使用谐波齿轮。
谐波齿轮传动机构由刚性齿轮、 谐波发生器和柔性齿轮三个主要零件组成, 如图5所示。 工作时, 刚性齿轮固定安装, 各齿均布于圆周, 具有外齿形的柔性齿轮沿刚性齿轮的内齿转动。
柔性齿轮比刚性齿轮少两个齿, 所以柔性齿轮沿刚性齿轮每转一圈就反方向转过两个齿的相应转角。 谐波发生器具有椭圆形轮廓, 装在谐波发生器上的滚珠用于支承柔性齿轮, 谐波发生器驱动柔性齿轮旋转并使之发生塑性形。转动时, 柔性齿轮的椭圆形端部只有少数齿与刚性齿轮啮合, 只有这样, 柔性齿轮才能相对于刚性齿轮自由地转过一定的角度。
假设刚性齿轮有100个齿, 柔性齿轮比它少2个齿, 则当谐波发生器转50圈时, 柔性齿轮转1圈, 这样只占用很小的空间就可得到1∶50的减速比。
由于同时啮合的齿数较多, 因此谐波发生器的力矩传递能力很强。在3个零件中, 尽管任何2个都可以选为输入元件和输出元件, 但通常总是把谐波发生器装在输入轴上, 把柔性齿轮装在输出轴上, 以获得较大的齿轮减速比。
图5谐波齿轮传动
直线驱动和旋转驱动的选用和制动
1. 驱动方式的选用
在廉价的计算机问世以前, 控制旋转运动的主要困难之一是计算量大, 所以, 当时认为采用直线驱动方式比较好。 直流伺服电机是一种较理想的旋转驱动元件, 但需要通过较昂贵的伺服功率放大器来进行精确的控制。例如,在1970年,尚没有可靠的大功率晶体管, 需要用许多大功率晶体管并联, 才能驱动一台大功率的伺服电机。
今天, 电机驱动和控制的费用已经大大地降低, 大功率晶体管已经广泛使用, 只需采用几个晶体管就可以驱动一台大功率伺服电机。同样, 微型计算机的价格也越来越便宜,计算机费用在机器人总费用中所占的比例大大降低,有些机器人在每个关节或自由度中都采用一个微处理器。
由于上述原因,许多机器人公司在制造和设计新机器人时, 都选用了旋转关节。然而也有许多情况采用直线驱动更为合适, 因此,直线气缸仍是目前所有驱动装置中最廉价的动力源, 凡能够使用直线气缸的地方, 还是应该选用它。另外,有些要求精度高的地方也要选用直线驱动。
2. 制动器
许多机器人的机械臂都需要在各关节处安装制动器, 其作用是: 在机器人停止工作时, 保持机械臂的位置不变; 在电源发生故障时, 保护机械臂和它周围的物体不发生碰撞。
假如齿轮链、谐波齿轮机构和滚珠丝杠等元件的质量较高,一般其摩擦力都很小, 在驱动器停止工作的时候, 它们是不能承受负载的。如果不采用某种外部固定装置, 如制动器、夹紧器或止挡装置等,一旦电源关闭, 机器人的各个部件就会在重力的作用下滑落。因此, 为机器人设计制动装置是十分必要的。
制动器通常是按失效抱闸方式工作的, 即要松开制动器就必须接通电源, 否则, 各关节不能产生相对运动。
这种方式的主要目的是在电源出现故障时起保护作用, 其缺点是在工作期间要不断通电使制动器松开。
假如需要的话, 也可以采用一种省电的方法, 其原理是: 需要各关节运动时, 先接通电源, 松开制动器, 然后接通另一电源, 驱动一个挡销将制动器锁在放松状态。 这样, 所需要的电力仅仅是把挡销放到位所花费的电力。
为了使关节定位准确, 制动器必须有足够的定位精度。制动器应当尽可能地放在系统的驱动输入端, 这样利用传动链速比, 能够减小制动器的轻微滑动所引起的系统振动, 保证在承载条件下仍具有较高的定位精度。在许多实际应用中, 许多机器人都采用了制动器。
图6为三菱装配机器人Movemaster EX RV-M1的肩部制动闸安装图。
图6三菱装配机器人肩部制动闸安装图
(来源:中国传动网)