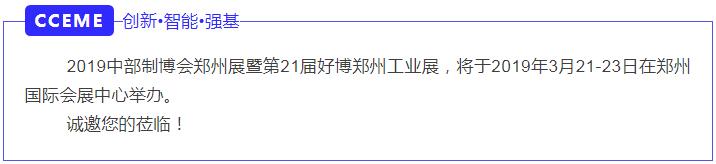
激光具有良好的单色性、相干性、平行性三大特点,因此特别适合应用于材料加工。国内传统的管材切割方法主要依靠手工锯割、锯床锯割、滚轮挤压、砂轮切割、气焊切割等,这些加工方法基本都存在切割效率低、工人劳动强度大等缺点,而激光切割凭借较快的加工效率、良好的加工效果等优点广泛应用于工业领域中。
随着科学技术和工业领域的发展,在航空器制造、工程机械、交通运输、石油化工、农牧机械等工业部门中,已经广泛采用管材制造零件。在实际生产中,管材有生产成本低、加工成形性好、结构件重量轻以及节省材料等优点,所以管材切割在工业领域中有着很重要的地位。由于管材的形状、尺寸及应用场合的不同,而且管材切割受加工质量等因素的制约,因此选用合理的加工设备、加工方法以及工艺措施是十分重要的。
管材切割存在着诸多不便,而国内传统的切割方法虽然也能达到应用效果,但是加工效率低下、加工效果较差,因此将管材切割与激光技术相结合,会使管材切割领域有着更加广阔的发展前景。
管材激光切割的现状和未来的发展
激光切割管材具有切口宽度窄、热影响区小、切割速度快、柔性好、切口光洁及无工具磨损等诸多优点。随着数控激光割管机的出现与发展,对于空间自由曲面和曲线的多种加工工艺的发展更能展现其独特的一面。激光切割管材时,不仅要求激光光斑相对于工件在三维空间按一定的轨迹运动,同时要求在整个加工过程中,激光光轴始终垂直于要切割管材的加工表面。对于可以进行自动调焦的数控光纤激光切割头,其喷嘴可以通过自动测量和控制系统对工件表面进行自动跟踪。生产实践表明,管材切割的关键在于最大程度的消除切割质量缺陷,从而满足管材的加工要求。对于复杂的管材进行穿孔、开槽、切边或侧凹等加工时,激光切割加工不仅比传统的加工方法更加快捷,而且能够极大的保证加工质量。
管材激光切割的概述
在加工过程中首先应该保证管材零件的割断,以获得所需长度的管材毛坯。国内传统的管材切割方法难以满足大批量生产的需要,而且这些传统加工方法加工出来的管材零件,切断面加工质量普遍不佳,有的甚至产生变形和压塌等加工缺陷。管材除了需要割断以外,有的还需要其他形式的加工,如:用于装饰和灯具的花纹切割,螺旋线、正弦、余弦线切割,打标等。这些形式的管材加工如果使用传统的加工方法,不但加工效率低下,而且难以达到理想的加工要求,有的甚至无法加工。
管材激光切割的优势
利用激光切割管材(包括正切、斜切、成形切割等)切口宽度一般为0.1~0.3mm,切割的位置和温度都能精确的控制,更加有利于实现生产的自动化和智能化,切割效率相较传统加工方式可提高8~20倍,加工费用降低70%~90%,可节省15% ~30%的材料损耗,而且激光切割的噪声小,对环境影响也较小。传统加工方式需要多道连续工序来完成加工的零件可以通过激光切割在同一台设备上实现。随着设备性能的不断完善以及加工工艺的不断改进,利用激光对管材进行高质量切割是可以实现的。
管材激光切割的未来发展趋势
激光切割采用非接触式的加工方式,在整个加工过程中,不会对管材的管壁有任何的压力作用,所以不会造成管材外表面的变形或者塌陷。同时,激光切割管材时,割缝热场复杂、冷却困难、切割熔渣易堵塞等原因造成切割难度加大,因此要加强对这些方面的深入研究。
激光切割对管材的材质、外形、尺寸、加工环境等要求的自由度很大,它的空间控制性(射束的方向变化、旋转、扫描等)和时间控制性(开、关、脉冲间隔)优异,容易控制,又因为激光切割的精密性高、毛刺少,大大减少了后续处理所消耗的时间。当改变管材的直径或者形状时,只需要修改程序就行,因此对管材切割软件进行开发就极具研究价值。激光切割系统和计算机数控技术相结合,可以构成高效的自动化设备,为优质、高效、低成本的加工开辟新的道路。
为了提高管材切割的工作效率,使用管材激光切割自动生产线才是最有效的生产方式。如何使用管材切割自动生产线进行激光切割呢?首先,聚焦之后的激光光束,必须保证与管材切割自动生产线上的被切割管材同步运行;其次,要求聚焦之后的激光焦点相对于被切割管材能旋转一周,且激光光束轴始终与管材的轴线垂直相交,在切断过程中,管材切割生产线的激光光束跟随被切割管材一起运动。这些同步运动必须通过专门的控制系统进行控制,所以对管材激光切割自动生产线的研究也有着很重要的意义。
管材激光切割的关键技术
导光聚焦系统
激光切割设备中,导光系统的作用是把激光发生器输出的光束引导到聚焦光路的切割头上。对于激光切割管材,要得到高质量的切缝就需要聚焦光束的聚焦光斑直径小、功率高,这就使得激光发生器进行低阶模输出。
在进行管材激光切割时,为了获得较为细小的光束聚焦直径,激光的横模阶次要小,最好是基模。激光切割设备的切割头带有聚焦透镜的,激光光束通过透镜聚焦后,就能获得较小的聚焦光斑,这样就可进行高质量的管材切割。
切割头的轨迹控制
在管材切割中,被加工的管材属于空间曲面,形状比较复杂,如果用常规方法编程加工会有一定的困难,这就要求操作人员根据加工工艺要求,选择正确的加工路径以及合适的参考点,利用数控系统记录下各轴的进给情况以及参考点的坐标值,再通过激光切割系统的空间直线和圆弧插补功能,记录加工过程的坐标值,并生成加工程序。所以研究激光光束与切割管材的自动垂直功能也是管材激光切割的重要技术内容之一。
激光切割焦点位置的自动控制
为了保证激光切割管材的切割质量,可以通过自动测量和控制装置使焦点相对工件表面的垂直方向不变,这是激光切割管材的关键。目前,我们通过对激光焦点位置的控制与激光加工系统直线轴(X-Y-Z )的一体化,使激光切割头的运动更加轻巧灵活,而且对焦点的位置都能了如指掌,避免了切割头在加工过程中与切割管材或者其他物件发生碰撞。
主要工艺参数的影响
激光切割管材在当今工业社会的应用越来越广泛,所要切割的管材也越来越多样化,且管类零件自身也有其复杂性,因此根据切割管材的材质、形状和加工要求,选择合适的激光切割工艺参数,获得最佳的切割效率和切割质量,成为所有激光切割系统用户最关心的问题。
⑴光功率的影响。
对于连续波输出的激光发生器来说,激光功率的大小会对激光切割产生重要的影响。理论上来说,激光切割管材设备的激光功率越大可获得的切割速度越大,但是结合管材自身的特点,最大的切割功率并非最佳的选择。当提高切割功率时,激光自身的模式也发生变化,这就会影响激光光束的聚焦。在实际加工中,我们常常会选择在小于最大功率的情况下,让焦点获得最高的功率密度,从而保证整个激光切割的效率与切割质量。
⑵切割速度的影响。
激光切割管材时必须保证切割速度在一定的范围内才能获得较好的切割质量。如果切割速度偏慢,过多的热量就会堆积在管材表面,热影响区变大,割缝变宽,排出的热融材料烧灼切口表面,使得切口表面变得粗糙。当切割速度加快时,管材圆周平均切缝宽度变小,而且被切割管径越小这种影响越明显。随着切割速度的加快,激光作用的时间缩短,管材吸收的总能量变少,管材前端温度下降,割缝宽度减小,如果切割速度过快,会出现管材割不穿或者割不断的情况,从而影响整个切割质量。
⑶管径大小的影响。
激光切割管材时,管材自身的特性对加工过程也会产生很大的影响。例如圆管管径的大小对加工质量有着明显的影响,通过对激光切割薄壁无缝钢管的研究发现,激光切割管材设备在各项工艺参数保持不变的情况下,管径不断增加切缝宽度也会不断增加。
⑷辅助气体的种类与压力。
切割非金属和部分金属管材时,可以使用压缩空气或者惰性气体(如氮气)作为辅助气体,而对于大多数金属管材则可以使用活性气体(如氧气)。在确定辅助气体的种类之后,确定辅助气体的压力大小也显得极为重要。当以较高的速度切割管壁厚度较小的管材时,则应提高辅助气体的压力,以防止切口出现挂渣;当切割管壁厚度较大或者切割速度较慢时,应适当降低辅助气体的压力,以防止出现管材割不穿或者割不断。
在激光切割管材时,光束焦点所处的位置也十分重要。切割时焦点位置一般在切割管件的表面位置,当焦点处于较好位置时,割缝最小,切割效率最高,同时获得的切割效果也最好。大多数情况下,光束焦点调整到喷嘴下方,喷嘴与管材表面的间距大约为1.5mm。与此同时,激光脉冲波形、光输出模式等因素也都对切割效果产生一定的影响。
结束语
激光切割管材离不开硬件─激光切割系统(包括激光发生器)和软件─激光切割工艺这两方面技术的支撑。从硬件来看,未来的激光割管机会朝着高速度、高精度、高自动化、柔性化、功能多样化的方向发展;从软件来看,未来的激光切割会与数控技术不断结合,以开发出新的软件,因此对激光切割工艺数据的收集与整理,建立和完善专家系统,对整个激光切割行业的发展都具有重要意义与研究价值。
——节选自《钣金与制作》2018年第7期
(来源:钣金与制作)